Lift safety: what are the repercussions of getting it wrong?
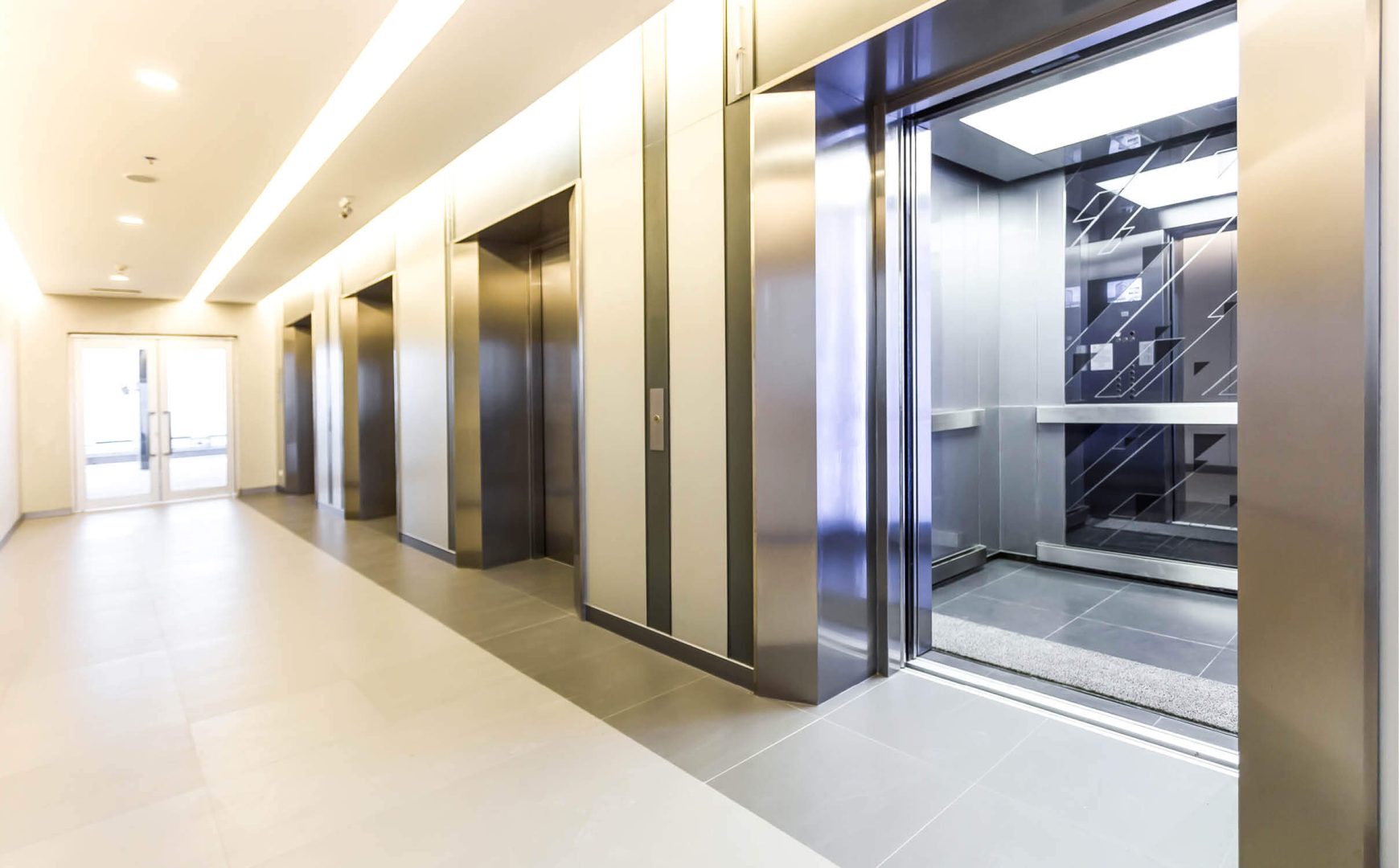
Recent incidents involving lift accidents serve as a stark reminder to employers to watch out for uncommon health and safety risks.
In the past couple of weeks, two significant prosecutions relating to serious accidents involving lifts have been reported. For those in the health and safety profession, it’s not unusual to see reports about fork lift trucks, but incidents with fixed lifting equipment are more surprising.
In the more serious of the two cases, a care home firm in Flintshire, Wales has been fined £90,000 after one of its staff – a newly-recruited care home manager – fell down a lift shaft.
The Care Home Operator was found guilty of four health and safety breaches at Mold Crown Court after their manager was seriously injured in the incident.
There is an uncanny similarity to a frequently quoted incident from the 1990’s, R v Gateway Foodmarkets Ltd (1996), where an employee also fell down a lift shaft through an unsecured hatch and died.
Besides this, last year, Europe’s biggest regional airline Flybe was fined £100,000 after a worker fell into a lift shaft at Exeter Airport.
About the recent case
In the more recent case, just three days after starting her job as manager of the care home, the injured person was alerted to a fault with the home’s lift, which had not dropped fully to ground floor. After opening the lift door on the first floor using an emergency key, which she had been directed to by another staff member, the manager fell down the shaft and sustained serious injuries.
An expert witness stated that the lift’s emergency release keys should be stored in a secure location for use only by authorised personnel. That would include people trained in the specific task of releasing someone who is stuck in the lift, or managers who are passing the release keys to such an authorised person. He went on to say, “I’d expect there to be a safe system of securing keys. [On this occasion] there was no reason to use a release key in my opinion – there wasn’t someone stuck. I see no evidence that the injured party was trained in the use of the release key.” Mrs Carter confirmed to the court that she hadn’t been trained in the use of the key.
In sentencing the Judge said: ‘The facts of this case serve to underline the high standard imposed on companies like the defendant company.” He said the systems the employer had in place regarding the lift were “inadequate”.
In addition to the £90,000 fine for the charge of failing to ensure the health and safety of employees, Judge Parry also ordered the employer to pay an additional £85,000 costs.
Fortunately, the second report was injury free but again highlights the business risk and potential fines associated with failing to adhere to basic H&S legislation and well established practices.
The second recent breach in lift safety
Separately to this case, a Birmingham tyre firm and its landlord have been fined a total of £43,333 at Birmingham Magistrates’ Court after pleading guilty to breaching health and safety legislation.
Birmingham City Council brought the prosecution following the discovery that a faulty tyre lift – which had already received a Prohibition Notice during an earlier inspection – had been switched back on and used again.
The initial routine inspection on 14 February 2019, found that a large platform lift at the tyre fitters was dangerous. The safety gate was missing and a safety interlock and mains control panel had been bypassed, resulting in the lift receiving a Prohibition Notice. Some months later, whilst inspecting another business, the health and safety inspector found the mains power to the lift had been switched back on and the lift had been used without the defects rectified.
The tyre company was prosecuted under section 2(1) of the Health and Safety at Work Act. However, the landlord of the premises was also brought to court.
Explaining the decision to prosecute the landlord as well as the occupying business, a spokesperson for Birmingham City Council said: ‘The lift – the plant – is the property of the landlord. It had a duty under section 4(2) of the Health and Safety at Work Act.”
At a hearing a Birmingham Magistrates’ Court, the tyre company was fined £26,677 and ordered to pay £3,751 in costs and £170 victim surcharge. The landlord was fined £16,666 and ordered to pay costs of £4,000 and a £170 victim surcharge.
The Health and Safety Executive (HSE) says that passenger lifts and combined goods and passenger lifts in workplaces that are primarily used by people at work should be subject to periodic thorough examination and inspection. This is required by Lifting Operations and Lifting Equipment Regulations (LOLER) and the Provision and Use of Work Equipment Regulations (PUWER) legislation.
How to ensure your business does not fail when it comes to lift safety
It is essential that all lifts are properly maintained and subjected to a thorough inspection by a competent person. Failure of the lift may result in serious injury and even death.
Anyone with responsibility for lifting equipment should:
- Arrange thorough examinations for all lifts at a frequency specified by the competent person.
- Retain a report/certificate that gives information on the safety of the lift.
- Maintain the lifts in accordance with manufacturer’s or installer’s instructions, and keep an up-to- date maintenance log.
- Instruct staff in their safe use, including emergency procedures associated with the lift.
- Train key staff in the procedures to be taken in the event of a lift breakdown and when people need to be released.
- Train key staff to carry out routine safety checks.
- Keep all moving parts of the lift machinery guarded.
- Prevent unauthorised persons from entering the lift plant room.