Employers may not be controlling Hazardous Substances
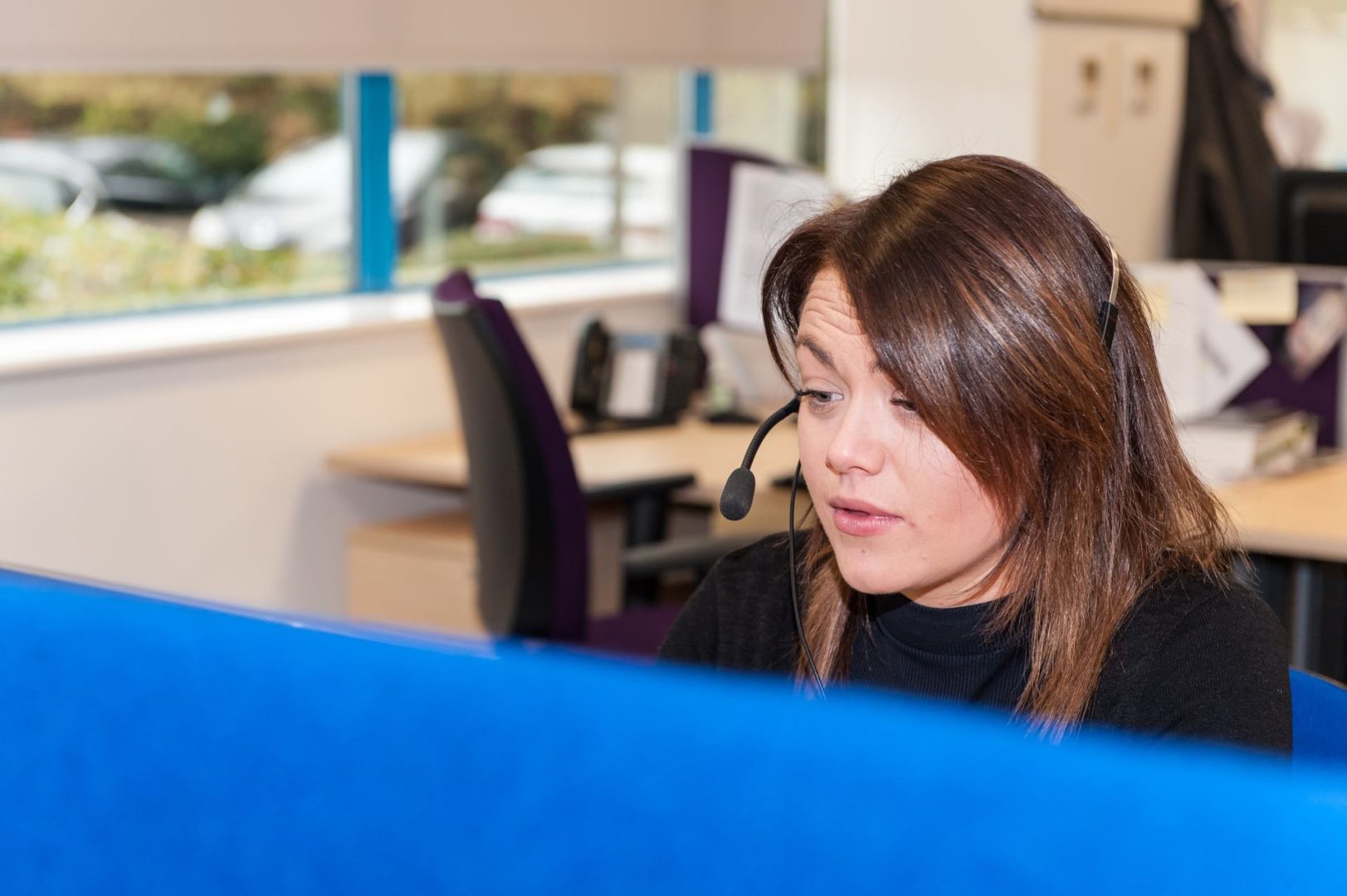
Many employers are unaware that some of the substances they use could result in their employees suffering adverse health effects.
One of the most common failings identified our team of Health & Safety professionals relates to the management of Substances Hazardous to Health.
The information gathered by employers on this topic is often out dated, which means that their Health & Safety assessments could no longer be suitable or sufficient if the supplier’s information, ingredients or exposure levels have changed.
So how can you make sure your employees are safe and that you are adhering to Health & Safety regulations? Here’s our quick guide…
Regulatory Requirements
There are a number of regulations relevant to the storage and use of chemicals in the workplace. The 3 that apply to all employers are:
- REACH: Registration, Evaluation, Authorisation & restriction of Chemicals (REACH)
- CLP: Classification, Labelling and Packaging of Substances and Mixtures (CLP Regulation), adopting in the EU the Globally Harmonised System (GHS)
- COSHH: Control of substances hazardous to health
The Health and Safety at Work etc Act also places general duties on employers to ensure the Health, Safety and Welfare of their employees.
REACH: Registration, Evaluation, Authorisation & restriction of Chemicals (REACH)
REACH is a European Union regulation concerning the Registration, Evaluation, Authorisation and restriction of Chemicals. It came into force on 1st June 2007 and replaced a number of European Directives and Regulations with one single system.
As end users of a product most employers will not be directly affected by these Regulations.
However, the regulations require companies that use chemicals to use them in a safe way, and according to the information on risk management measures passed down the supply chain from the manufacturers and distributors.
There is also an opportunity to pass information about use back to manufacturers so that this can be taken account of when assessing the risks of chemical used.
The CLP Regulation
European Regulations on classification, labelling and packaging of substances and mixtures came into force on 20 January 2009 and is known by its abbreviated form, ‘the CLP Regulation’ or just plain ‘CLP’.
These regulations adopt the United Nations’ Globally Harmonised System on the classification and labelling of chemicals (GHS) across all European Union countries, including the UK.
The most obvious changes brought about by these regulations are changes to some of the product descriptions and a new set of hazard pictograms. These changes should now be fully implemented and Safety Data Sheets from suppliers will include the new pictograms.
Anyone who has previously completed COSHH Assessment will also notice the change from Risk Phrases and Safety Phrases to Hazard Statements and Precautionary Statements
COSHH: Control of substances hazardous to health
The Control of Substances Hazardous to Health (COSHH) Regulations are the UK Regulations that require employers to control substances that could adversely affect the health of their employees, and others.
Assessing the risk of ill health from exposure to manufactured substances requires access to information from suppliers which they must provide to comply with REACH and CLP legislation.
However, there are often ill health effects associated with none manufactured products such as silca dust, wood dust, and bodily fluids
Employers can prevent or reduce workers exposure to hazardous substances by:
- finding out what the health hazards are;
- deciding how to prevent harm to health (risk assessment);
- providing control measures to reduce harm to health;
- making sure they are used ;
- keeping all control measures in good working order;
- providing information, instruction and training for employees and others;
- providing monitoring and health surveillance in appropriate cases;
- planning for emergencies.
Steps to Effectively Controlling Hazardous Substances in the Workplace
1) Identify Substances that are used, or which employees come into contact within your workplace, include manufactured and naturally occurring substances.
2) Maintain a list or inventory of these substances.
3) Determine if substances are hazardous to health. This information MUST be provided by manufacturers of substance in the form of a data sheet and up to date copies should be obtained from suppliers. For non-manufactured substances the Health and Safety Executive provide employers with access to information on the hazards and risks that should be considered.
4) Using information from data sheets, HSE, trade groups etc. determine the likelihood that the health of staff, and others, coming into contact with substances will be adversely affected. This requires employers to consider the nature, form and properties of each substance and how they them.
5) Identify if any substances used have specified exposure limits, stated on the Data Sheet for manufactured Substances, and determine if monitoring is required to ensure exposure is below these limits.
6) If there is a risk to health then;-
- Assess the risk.
- Decide what precautions to take.
- Prevent or adequately control exposure.
- Ensure that control measures are used and maintained.
- Monitor the exposure.
- Carry out appropriate health surveillance.
- Prepare plans and procedures to deal with accident, incidents and emergencies.
- Ensure employees are properly informed, trained and supervised.
All too often we find employers look to use PPE (Personal Protective Equipment) to protect against hazardous substances.
COSHH Regulation 7 outlines a Hierarchy of control to minimise the risk associated with hazardous substances.
Firstly look to prevent exposure by:
1. Eliminating the substance.
2. Substitution with a substance less hazardous to health.
If it is not possible to prevent exposure then minimise the exposure to lowest possible level by:
1. Total enclosure of the process, therefore removing exposure.
2. Limiting the area of contamination by enclosing a process or containing a spill.
3. The use of LEV (Local Exhaust Ventilation) to remove airborne substances from the workplace.
4. Dilution Ventilation using a high number of air changes per hour to keep contamination of the atmosphere to a minimum.
5. Reducing the period of exposure keeping substances in sealed containers when not in use, positioning control systems outside of potentially contaminated areas reducing the time operatives need to be in these areas etc.
6. Providing suitable PPE.
For further guidance and assistance, you can book a consultation anytime or refer to our handy employer resources.
By Phil Barker